Tungsten Trioxide Desulfurization Catalyst
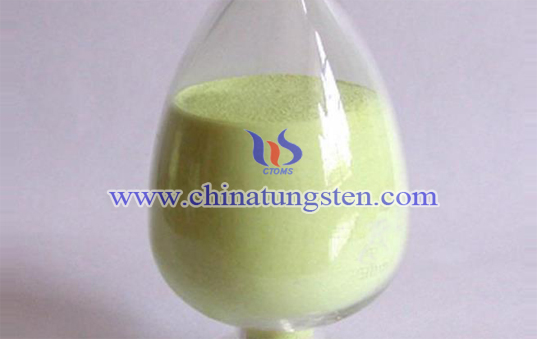
Tungsten Trioxide Desulfurization Catalyst
Sulfur is a harmful element, the tail will bring great harm when high-sulfur coal used both in the gasification or combustion; such as high sulfur content coal as a fuel, the sulfur dioxide gas produced will not only cause severe corrosion of boiler pipes, but also serious pollute the atmosphere; when high-sulfur coal used in the preparation of semi-water gas, it will cause catalyst poisoned since the gas hydrogen sulfide and other gases are difficult to clean off. In the normal coal burning process, organic sulfur and sulfur compounds can be decomposed completely in 800~900°C; however, sulfur in the sulfate begins to decompose at the temperature of 1100~1200°C, a higher oven temperature is needed for ensuring that various forms of sulfur in coal are able to break down.
The catalyst can significantly increase the rate of reaction and keep its chemical nature and number not changed before and after the reaction. whether the chemical reaction can be carried out or not is not only requires the change of free energy, but also according to the energy barrier, because if the energy barrier is really high, more energy need to provide for completing the reaction, wherein the energy barrier is called activation energy, and the catalyst is playing the role of reducing the activation energy of the reaction. The key of catalyst changing the rate of reaction is that it can change the response pathway from a high energy barrier to a lower energy barrier needed, thus to reduce the activation energy.
Tungsten trioxide, as a main active material, is uniformly dispersed on the desulfurization catalyst carriers, can reduce the activation energy of the reaction; Furthermore, the tungsten trioxide can alleviate the curing catalyst poisoning and improve the anti-sintering ability, thereby increasing the activity and the efficiency of desulfurization.