Tungsten Oxide Denitration Catalyst
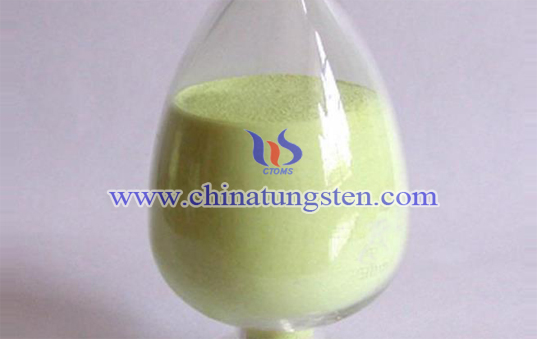
Tungsten Oxide Denitration Catalyst
Denitration catalyst nano-titanium dioxide is a kind of titanium dioxide, the powder which doped with tungsten trioxide, vanadium pentoxide. The catalyst powder may be supported on a stainless steel plate, ceramic, glass fiber base material, and then shaped in a plate, corrugated honeycomb or plate, finally integrated in the steel to composite of the overall denitration reactor. Denitration catalyst comprising tungsten with titanium dioxide has the nice properties such as high hydrophilicity, strong adsorption, high specific surface area and catalytic activity, stable surface area when sintered under high temperature at 600℃, no secondary pollution, thus mainly used for denitration, which the denitration rate can up to more than 95% under the condition of 100% flue gas.
SCR is the most effective denitration technology currently, the denitration catalyst containing tungsten trioxide is a denitration catalyst with excellent performance. Compared with traditional SCR catalyst, this catalyst has a larger surface area, particle uniformity, low sulfur content and high catalytic activity, and thus having a stronger catalytic reduction. Denitration catalyst titanium dioxide containing with tungsten is mainly used for the manufacture of a denitration catalyst, a good carrier material for SCR denitration catalyst, mainly dealing with nitrogen oxides, specifically for waste incineration and chemical plants, oil refineries, coke, flue gas treatment, and automotive glass factory, ship exhaust gas treatment required for denitration catalyst manufacturing.
If the catalyst exposures at 450℃ for a long-term, it will easy to cause prone catalyst sintered, thus leads to the TiO2 catalyst particle changed, specific performance like that the surface area reduced, activity decreased, but the introduction of tungsten trioxide can reduce the sintering of catalyst at maximum. Furthermore, tungsten trioxide evenly distributed in the surface of titanium dioxide, and catalyst efficiency has been further improved after it combined with vanadium pentoxide.