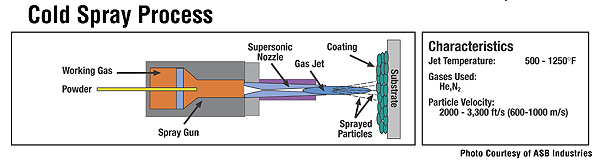
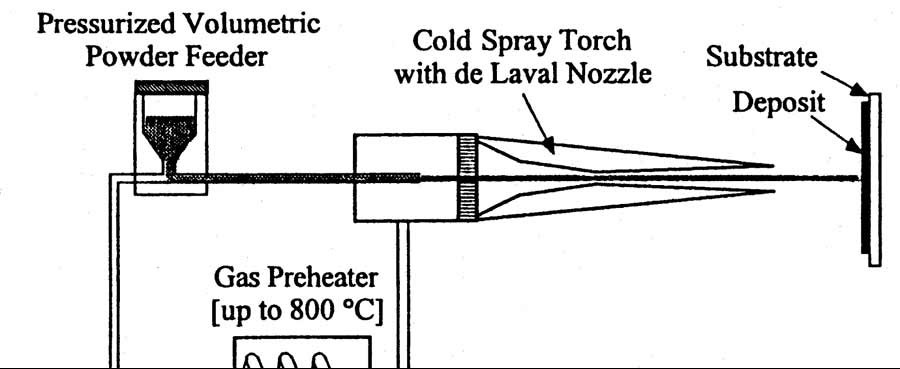
In the 1990s, cold spraying (often called gas dynamic cold spray) has been introduced. The method was originally developed in Russia with the accidental observation of the rapid formation of coatings, while experimenting with the particle erosion of the target exposed to a high velocity flow loaded with fine powder in a wind tunnel. In cold spraying, particles are accelerated to very high speeds by the carrier gas forced through a converging–diverging de Laval type nozzle. Upon impact, solid particles with sufficient kinetic energy deform plastically and bond metallurgically to the substrate to form a coating. The critical velocity needed to form bonding depends on the materials properties, powder size and temperature. Soft metals such as Cu and Al are best suited for cold spraying, but coating of other materials (W, Ta, Ti, MCrAlY, WC–Co, etc.) by cold spraying has been reported.
The deposition efficiency is typically low for alloy powders, and the window of process parameters and suitable powder sizes is narrow. To accelerate powders to higher velocity, finer powders (<20 micrometers) are used. It is possible to accelerate powder particles to much higher velocity using a processing gas having high speed of sound (helium instead of nitrogen). However, helium is costly and its flow rate, and thus consumption, is higher. To improve acceleration capability, nitrogen gas is heated up to about 900 C. As a result, deposition efficiency and tensile strength of deposits increase.
If you have any interest in our products, please feel free to contact us by email: sales@chinatungsten.com or by telephone:
+86 592 5129696.
More info>>
1.Tungsten Powder
2.Catalog of Tungsten Powder
4.Terms of Powder Metalury
5.High_Velocity_Oxyfuel_Spraying
|